Comprehensive Modular Building Buyer’s Guide
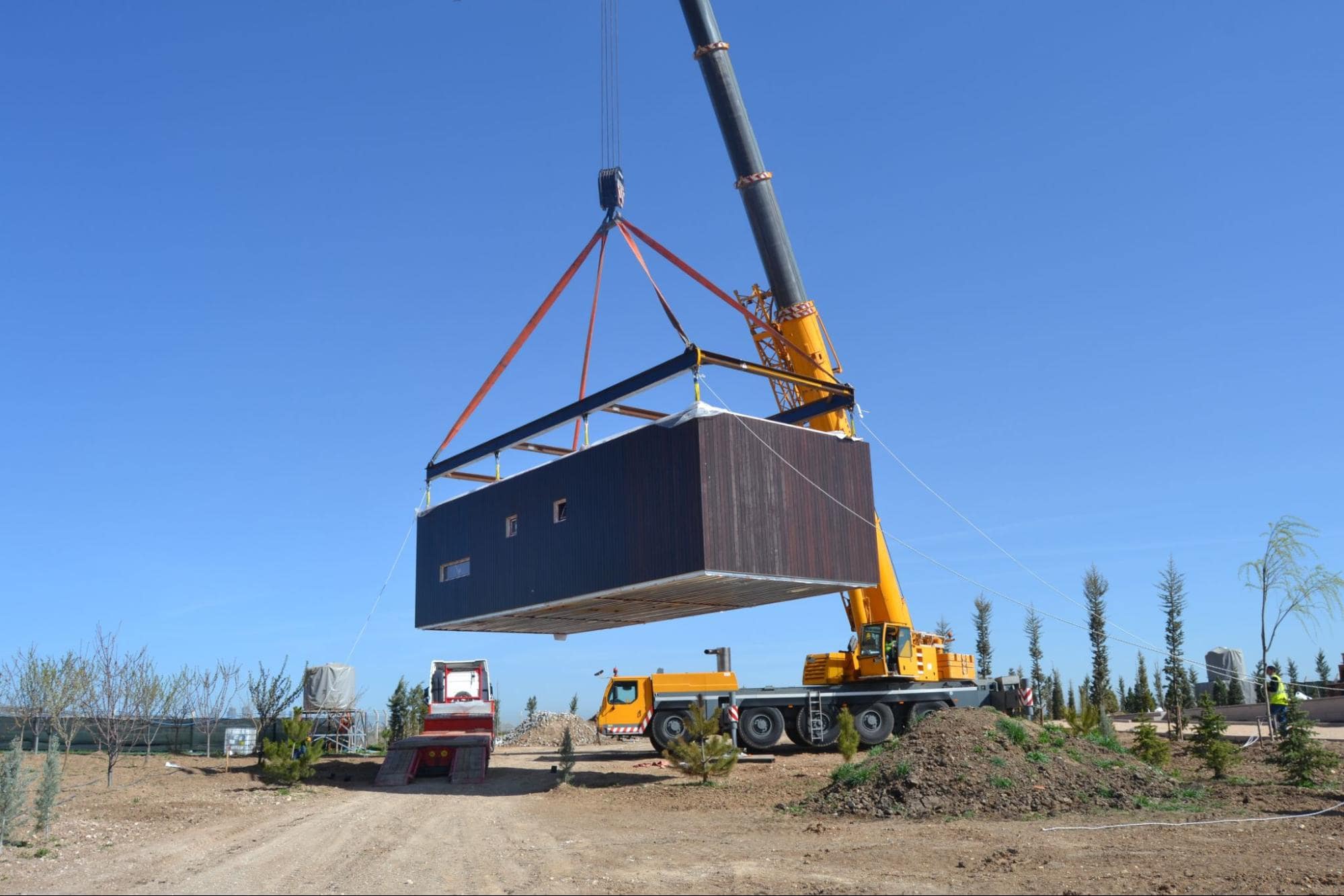
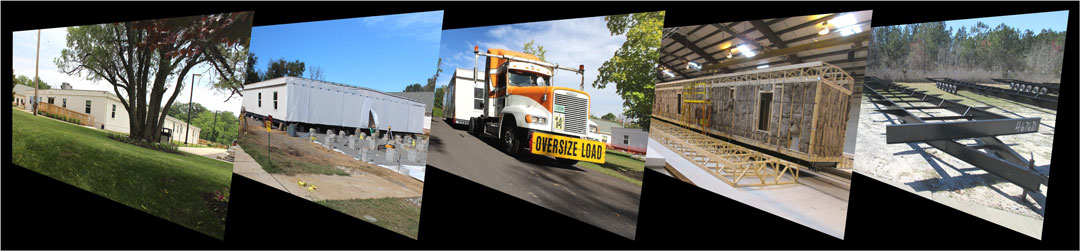
Modular buildings can be a complicated subject, and many people aren’t exactly sure what they are. If you’re considering modular construction for your organization, it’s important to understand the details so you can make an informed purchase. Our comprehensive modular building buying guide will teach you all there is to know about modular construction. You’ll also get a better understanding of what to expect out of your modular project from beginning to end.
If you already know the information you’re looking for, you can use the links below to jump directly to that content:
What is Modular Construction?
Is Modular Construction the Right Solution for Your Situation?
What Are the Capabilities of Modular Construction?
What Are the Limitations of Modular Construction?
What Are the Benefits of Modular Buildings?
Which Industries Can Benefit From Modular Construction?
What Are the Differences Between Temporary and Permanent Modular Buildings?
Should You Purchase or Lease a Modular Building?
What Building Materials Are Used in Modular Construction?
How Much Do Modular Buildings Cost?
What’s the Timeline for Modular Construction?
What Are the Steps Involved in Getting a Modular Building?
Factors to Consider Before Requesting a Quote for a Modular Building

What Is Modular Construction?
Here’s a quick snapshot of the key characteristics of modular construction:
• Modular buildings are essentially traditional buildings that are constructed off-site in a factory, rather than built from the ground-up on site.
• They’re built using assembly line techniques to prefabricate individual sections (modules) of a building.
• Off-site fabrication allows the construction site to be prepared simultaneously, rather than each phase being performed consecutively.
• Modular buildings can be as little as a few hundred square feet to as large as tens of thousands of square feet.
• They’re built with standard materials used in traditional construction.
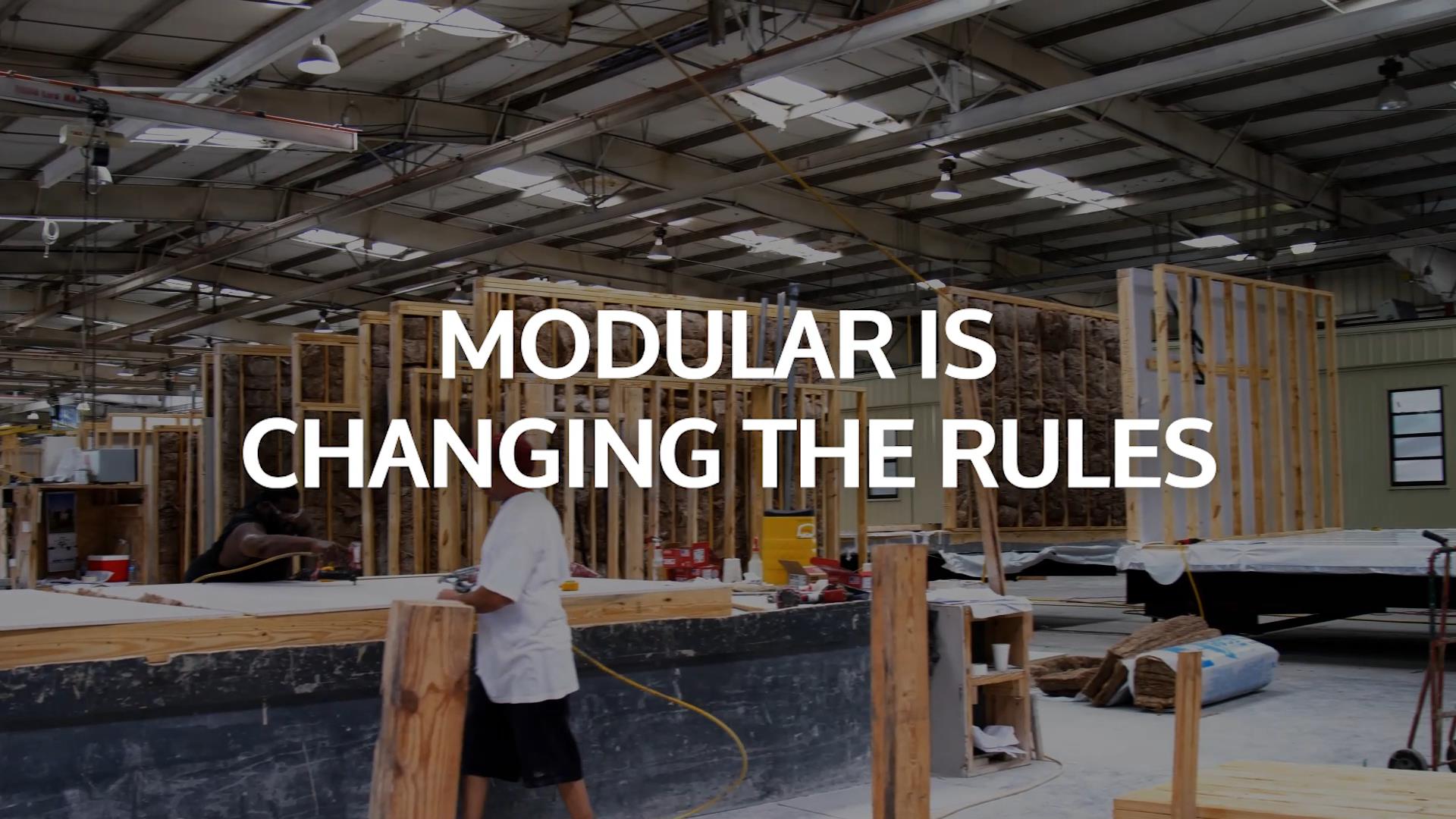
Is Modular Construction the Right Solution for Your Situation?
Modular construction is an excellent choice in a wide variety of situations. Here are a few of the most common reasons your organization might turn to modular:
• Your organization is growing and you need additional space.
• You have old buildings that need to be replaced.
• You need swing space during renovation projects.
• You need workspace for on-site contractors.
• You have temporary buildings, but need permanent ones.
• You’re a new organization.
What Are the Capabilities of Modular Construction?
There have been significant advancements in the technology, engineering, and design of modular buildings over the past few years. These have accelerated the need for new markets for permanent modular construction (PMC). Some companies are building multi-family housing, hotels, high rises, banks, and franchise restaurants meeting precise modular building specifications.
What Are the Limitations of Modular Construction?
Due to roof height limitations, modular buildings aren’t always viable solutions for gyms, auditoriums, or other high ceiling facilities. This is because over-the-road module transportation requires compliance with roof height regulations. They’re also not an ideal choice if you need extensive clear-span space with no supports.
What Are the Benefits of Modular Buildings?
The biggest advantage of modular construction over traditional construction is the accelerated building schedule and occupancy. Additional benefits of modular buildings include:
• Off-site construction is a cost-effective option for organizations of all sizes.
• Off-site construction is often more environmentally-friendly than traditional construction.
• There’s less disruption to operations and job sites, making modular a more convenient option.
• You can choose between temporary or permanent structures, which isn’t possible with traditional construction.
• Modular buildings meet applicable construction codes, including the International Building Code (IBC) and other applicable federal and state building codes and regulations.
• Modular buildings can be built to look like existing structures.
• Modular buildings minimize the use of internal resources and keep upfront capital expenses low.
Modular Building Process Explained | Step-By-Step
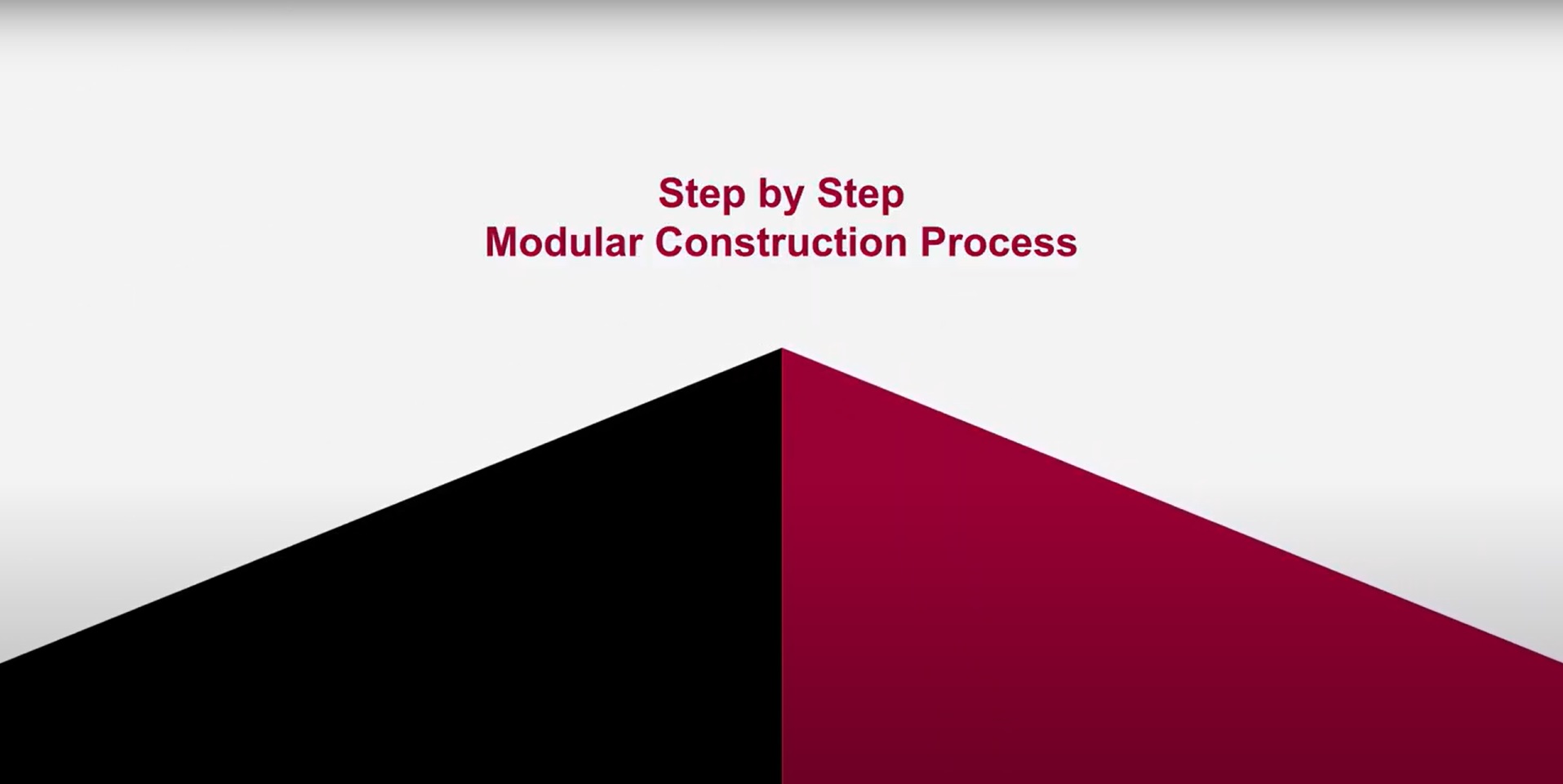
Which Industries Can Benefit From Modular Construction?
Due to their many benefits, modular buildings can satisfy the needs of organizations in almost any industry. Here are just a few industries that use modular:
• Banking & Financial
• Commercial
• Education
• Government
• Manufacturers
• Utilities
A few of the most common modular building types within these industries are:
• Classrooms
• Offices
• Medical clinics
• Restrooms
• Banks and credit unions buildings
• Laboratories
• Scale houses
What Are the Differences Between Temporary and Permanent Modular Buildings?
There are two main types of modular construction: temporary buildings and permanent buildings. Let’s take a closer look at each kind.
Temporary Modular Buildings
Temporary modular buildings are defined by their intended use, foundation design, and how they’re affixed to that foundation, not their structural design. In other words, a temporary building designed for relocation can still be affixed as a permanent building.
In most cases, temporary modular buildings are used as leased space for a predetermined period of time. Temporary buildings of any size can be delivered to a property, installed, and removed when no longer needed. Because they’re engineered and designed for relocation, temporary buildings can be repurposed and redeployed for use several times during their lifespan.
Temporary modular building foundations are specifically engineered so the modules can be disconnected and demounted easily. These concrete pier foundations are also relatively easy to disassemble and remove. They can be installed on a parking lot or plot of grass, and typically rise 2-3 feet above ground. Decks and ramps are installed at the entrance of temporary modular buildings for easy access.
With proper maintenance, temporary buildings can have a useful life of 20-30 years. The limit on useful life is primarily due to them being set up, disassembled, and relocated numerous times to various locations.
Permanent Modular Buildings
Permanent modular buildings are installed and affixed to foundations that are engineered and designed for long-term use. They’re often built as II-A, II-B, and V-B structures and can be framed in wood, steel, or concrete. With proper maintenance, they can have the same lifespan as traditional construction.
Because they’re most often set at grade level, permanent modular buildings require full perimeter foundation walls and interior concrete piers. While this option is more expensive, it eliminates the need for decking to exterior doors. Permanent modular structures are typically accompanied by ground-level accessibility, extensive stormwater management systems, sidewalks, and landscaping.
Should You Purchase or Lease a Modular Building?
Depending on your individual needs and situation, you may decide to lease your modular building. Leasing is your best option if:
• You don’t want to own the building for business reasons
• You intend to use the building temporarily
• You don’t want to spend the capital upfront to purchase a building
In most cases, you’ll want to lease a used building as opposed to a new one. This is because they’re already built and can be installed and occupied more quickly. They’re also more affordable than new buildings.
What Building Materials Are Used in Modular Construction?
Modular construction employs the same customary building materials that are used in traditional construction. There are an endless number of custom interior and exterior upgrade materials. Materials are often purchased in bulk to keep costs low and are stored under roof (often in climate-controlled areas), protecting them from drastic temperature swings and inclement weather.
How Much Do Modular Buildings Cost?
The customization level, structure type, and project complexity dictates modular building pricing. Each modular building has its own set of specifications, so prices can vary widely.
Sale prices for new V-B-type standard temporary modular buildings generally range from $75-130 per square foot. Custom buildings have a much wider price range, which can be anywhere from $150-400+ per square foot. This is due to the nearly endless customization options, from the engineered support structure to final finishes. Costs beyond the building itself can include permits, site work, foundations, delivery, installation, access systems, utility runs, and more.
If you’re looking to lease a standard temporary modular building, you’ll generally pay $1.20-1.75 per square foot per month. The lease term length and building size are the primary drivers behind the monthly rate you pay.
Which Factors Affect Overall Modular Building Pricing?
There are many factors that can affect the price you pay for your modular building. A few of the most common include:
• Location of water, sewer, and utilities
• Building size, customizations, and structure
• Site accessibility
• Exterior finishes
• Crane usage
• Surveillance & alarm systems
• Sprinkler systems
• Excavation & grading
• Site soil compaction
• Storm water management
What’s the Timeline for Modular Construction?
Each modular building project is different, but the time frame from start to finish is roughly 8-20 weeks. On the other hand, traditional construction for a similar project can take 6-12 months. Factors that can impact your schedule include:
• Building design changes
• Plan review and building inspection process
• Utilities being energized
• Decisions by committee
• Changes to original scope
• Sprinkler systems
• Site soil compaction
• Stormwater management
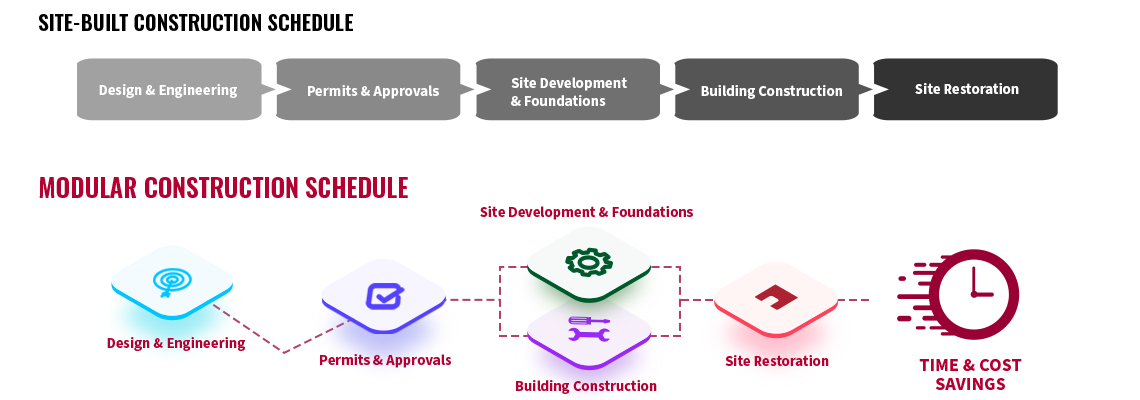
The Modular Manufacturing Process Explained
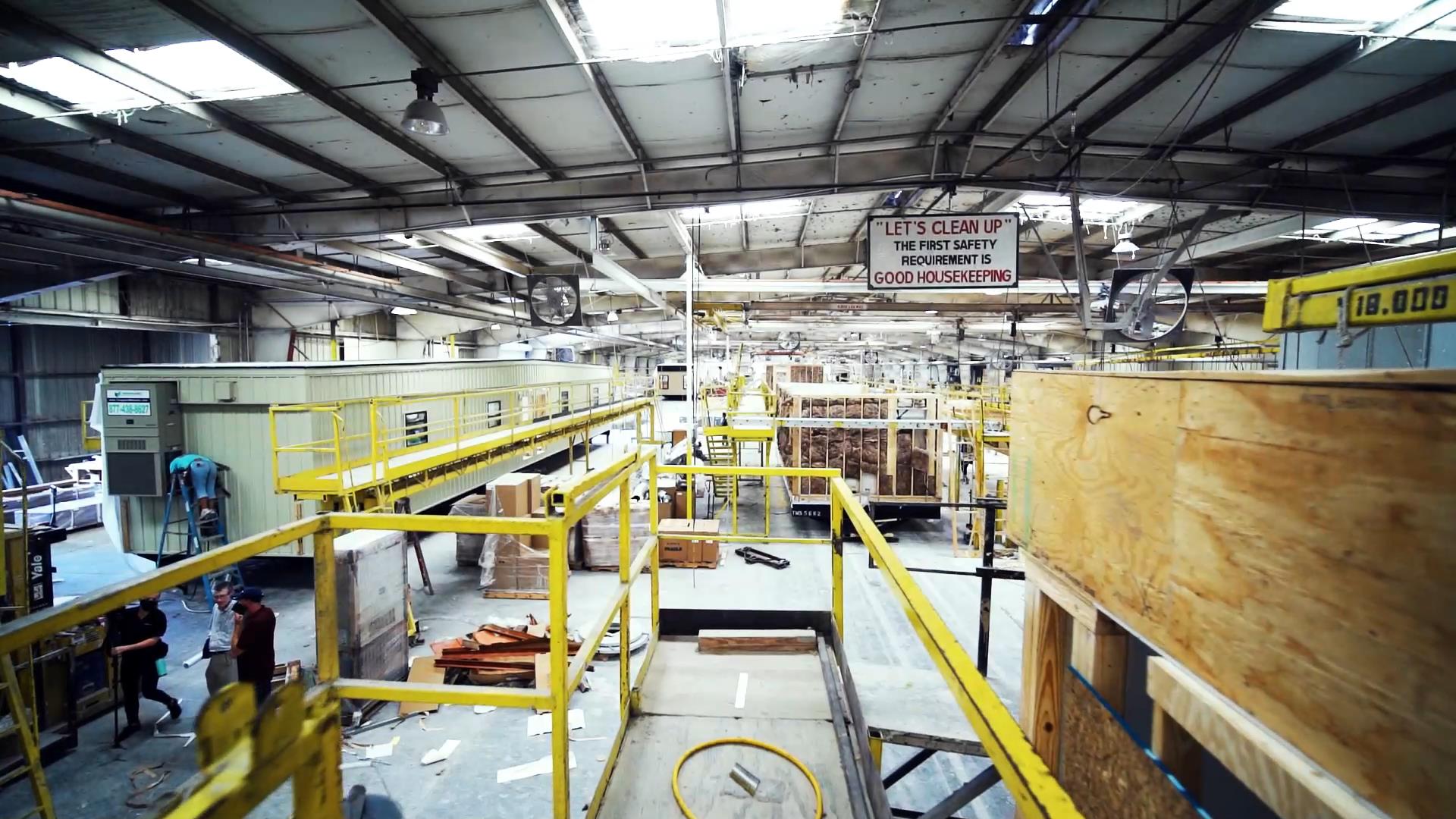
What Are the Steps Involved in Getting a Modular Building?
The ten steps below make up the process of getting a modular building from start to finish.
1. Property Identification
The site you choose is very important, as it directly impacts many other aspects of the process. Be sure to consider the grade (slope), soil compaction, site accessibility, and proximity to water, sewer, utilities, and existing structures. These considerations can have a significant bearing on the cost of your project, but they can be controlled in advance by selecting the right property.
You’ll also want to have a clear understanding of the municipality or local governing body and how easy or difficult they’ll be to work with. The permitting process and project inspections can impact the project schedule, sometimes substantially.
2. Building Design
Project owners typically partner directly with modular building dealers that have the ability to perform complete design-build projects. In other cases, they work directly with an architect to design their building. Both routes generally result in a high-quality structure built to your exact modular building specifications.
3. Formal Proposal
The formal proposal allows you to see everything in one place before signing a contract. A typical proposal may include delineation of responsibilities, pricing, project schedules, terms, drawings, and building specifications.
4. Permits & Approvals
In most cases, you’ll need to obtain the proper permits and approvals. However, these can also be secured by the modular dealer for an additional fee. It’s important to find out what local officials require as early in the process as possible, since permit application approval can take a significant amount of time. The length of the approval process typically depends on where your building will be located.
5. Contracts
There are as many different types of contracts as there are designs for modular buildings. Your contract form is typically determined by the size and scope of your project. Other than monthly rental invoices, most projects are billed either based on milestone achievements or monthly percentage of project completion.
6. Site Preparation
As your modular building is being built at an off-site factory, crews will work to prepare the job site for building delivery. This can include surveying, demolition, excavation, foundation work, utility installation, and more.
7. Plant Fabrication
Once your building design is approved, it will be constructed at your dealer’s modular building factory. The support structure, plumbing, electric, data, mechanicals, ductwork, insulation, doors, windows, interior finishes, and exterior finishes are often completed within the factory.
8. Modular Building Delivery
Once your modules are completed, the individual sections are transported to the job site by over-the-road truck in a predetermined order.
9. Installation
As the modules arrive on-site, they’re staged and prepared to be set in order on the completed foundation system. The sections are situated precisely on the foundation one at a time next to each other to ensure they line up properly.
Connections between walls, ceilings, electrical, data, plumbing, and ductwork are completed during installation at each mate line, which is where the modules meet up. This involves attaching the exterior weather-proofing and facade, along with completing the interior floor, wall, and ceiling finishes.
External connections are then made with utilities, water, sewer, alarm systems, and data lines (if applicable). The unit is energized for power, and the water is turned on. Access systems like decks, steps, ramps, and sidewalks are also installed. Paving, striping, restoration, and landscaping are also performed at the end of the installation process.
10. Occupancy
Once the required inspections are complete and the proper approvals are given, local authorities will issue a certificate of occupancy.
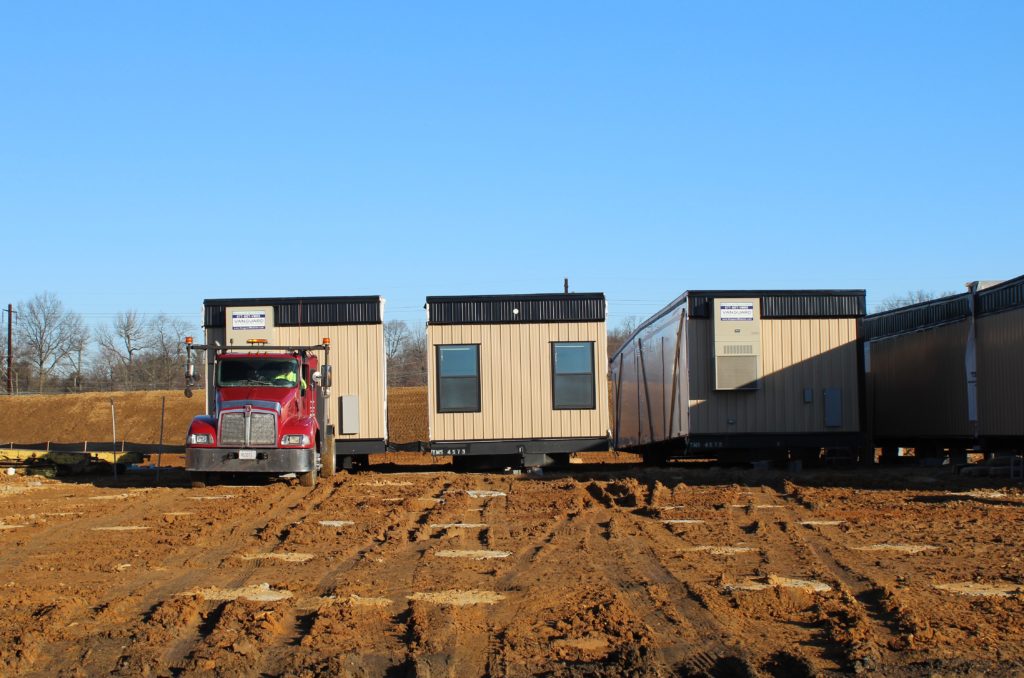
Factors to Consider Before Requesting a Quote for a Modular Building
There are a few things you should consider — but not necessarily have all the answers for — before requesting a modular building quote. Having more answers ahead of time can help move your project along more efficiently, though.
Here are a few things you might want to determine before contacting a modular building dealer:
• Your land availability (owned or leased)
• How much space you need (both occupancy and layout)
• Requirements of your project (aesthetics and security)
• Occupancy time frame and/or length of need
• Whether you plan to rent or own the facility
• Your budget and funding source