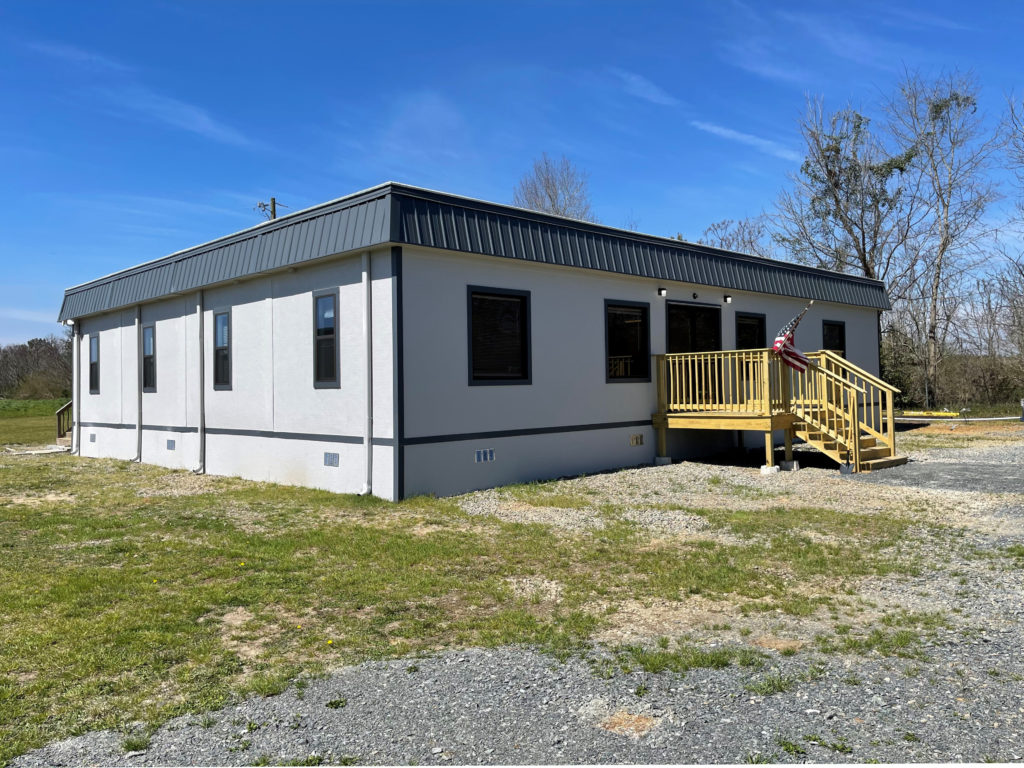
Do you worry about the durability and construction quality of modular buildings? Does it give you second thoughts about utilizing modular construction methods? Don’t worry.
Modular buildings are designed and constructed to meet the IBC (International Building Code) requirements for commercial buildings and applicable federal and state building codes. These are the same standards used to inspect and approve commercial buildings constructed using traditional building methods.
In this blog, we’ll answer a few more questions about modular building codes and explain how our process ensures all rules and regulations for modular buildings are constructed to meet or exceed all building code requirements.
Modular Building Codes & Guidelines
All buildings are designed to follow building codes at the state and federal levels. However, technically speaking, there isn’t a building code created specifically for modular buildings.
That being said, as we mentioned above, modular buildings are expected to follow the same building codes required of traditional site-built structures.
It’s important to keep in mind that in the United States, these codes are updated every three years with varied state adoption. Therefore, builders are responsible for staying up to date on any changes and ensuring they continue to meet the International Building Code (IBC).
Unlike building codes, guidelines are not required rules and regulations set by the International Code Council. However, understanding popular modular building guidelines can help people stay current with new building trends and address questions not yet covered by international building codes.
Even though there isn’t a designated modular building code, these buildings are still required to go through an inspection and permit process before construction starts, and before anything is occupied. We will discuss these inspections and permits in more detail later in the blog.
Are Modular Buildings Compliant with Building Codes?
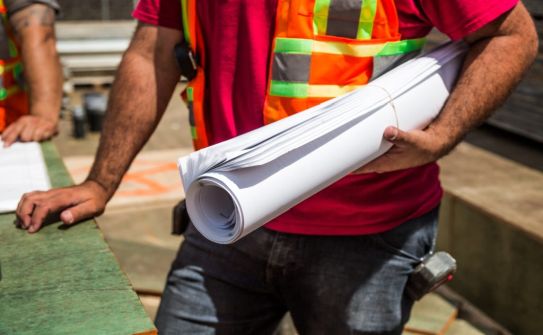
Modular designs and final buildings are inspected and approved based on IBC standards for:
- Structural design
- Roof assembly
- Foundation
- Means of egress
- Fire and smoke protection
- Life safety systems
- Electrical, mechanical, and plumbing
- Accessibility
- Energy conservation
Modular building inspections are completed at the time of manufacture and buildings are evaluated following the codes applicable to the location where the building will be installed.
If your modular building will be installed in Ohio but is built in Pennsylvania, it will be inspected to meet all building code requirements for Ohio.
In the many instances where a temporary modular building will be used in several locations, it will be evaluated and inspected to meet the building regulations for several states at once.
Modular Building Inspections
There are three steps in the modular construction process where buildings are evaluated and approved based on building code requirements. Buildings are inspected during the design phase, before delivery, and after final assembly.
When modular construction designs are complete, the drawings and specifications are sent to third-party engineers for review. They will inspect the designs to ensure all federal and state codes are met. Any necessary revisions will be made before the start of manufacturing.
Specialized inspections are also completed throughout the manufacturing phase as the individual building modules move down the assembly line. These quality control efforts allow non-compliant issues to be caught and corrected without affecting the other project areas.
Before construction begins, soil survey inspections are required on-site. These soil evaluations allow builders to determine the composition of the soil at the site. This ensures the ground will be able to withstand the upcoming construction tasks and the foundation of the building itself. In addition, these tests will provide insight into any harmful toxins in the soil before construction begins.
When construction is complete, the modules are inspected to ensure they comply with all applicable building codes. This inspection, like in the design phase, is carried out by a third-party partner.
Once all approvals have been passed, proof of compliance (which in most cases is a tag or a seal) is applied to each module. Only then can they be shipped to the build site for assembly.
Finally, after the modular building is assembled on-site, the last inspection must take place before the owner can take occupancy. Inspectors will look at:
- Site connections that hold the modules together
- Building foundation
- Site utility work
- ADA compliance
- Fire protection and suppression
- Life Safety
- Issues with the surrounding land, including water runoff
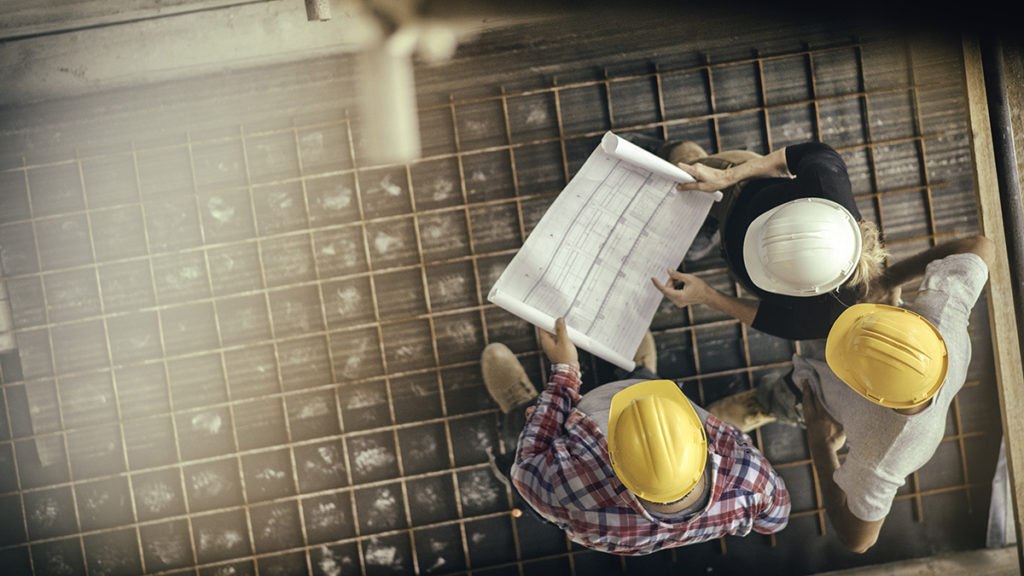
Modular Building Permits
Since some modular building permits take a long time to be processed, anywhere from days to months, it’s recommended to apply for them well in advance.
Building permits allow construction to officially begin. These will be sent to the proper local authorities and include the results from the soil tests, construction blueprints, and the structural foundation plan.
The next required permit is known as a utility permit. This provides approval to set up and use basic utilities such as plumbing and electricity. Lastly, final use and occupancy permits are needed when the modular building is completed to ensure the building is safe, up to code, and ready to be occupied.
Modular buildings undergo extensive review and compliance, which can seem daunting, but in the end provide users with the peace of mind that their building is durable, safe, and well-constructed.
Reach out to one of our experts in your area to learn more about the safety, and durability of today’s modular spaces.
Ready to solve your space needs?
Modular buildings are the way to go. Request a quote or contact us today to get the conversation started. We’d love to talk to you about how modular can meet — and exceed — your needs.