Modular Building Maintenance Inspection Checklist & What to Know About Permitting
This blog is a rewrite and combination of two Modular Building Inspection blogs. This blog was originally published on November 30, 2021 and updated on November 2nd, 2022.
Just like traditionally-built structures, modular buildings require regular inspections and maintenance to ensure a long lifespan. We’ve created a building repairs checklist for your modular structure, and now we’re giving you a modular building maintenance inspection checklist.
Your modular structure is a big investment to your organization, and this building maintenance inspection checklist is designed to extend your structure’s lifespan for the entirety of your project.
Plus, we’ve provided information about modular building inspections and permitting to put these maintenance tasks in context. We’ll start by reviewing the benefits of basic building maintenance for modular structures.
Routine Building Maintenance Checklist for Modular Structures
There are many benefits of creating - and sticking to - a modular building maintenance inspection checklist, including:
- Minimizes dealer service requests.
- Extends the useful lifespan of your modular building and keeps it looking like new.
- Helps prevent weather-related damage and ensures your building can handle the elements.
- Allows you to catch minor issues before they become major, expensive problems.
While you may be able to make some fixes on your own, contact your dealer if routine maintenance uncovers the need for more complicated repairs.Listed below, we will cover some of the top places to inspect and maintenance tasks to do on your own.
Each maintenance task should be completed either monthly, seasonally, or annually. We’ll be sure to highlight how often to do each job in the descriptions below.
Before we get into each area, here are maintenance guidelines that should be completed routinely.
Every Month
- Change filters in the HVAC units.
- Remove any objects blocking your skirting vents or your air return vents.
- Check indoor and outdoor light bulbs.
Every Year
- Replace batteries in the smoke detectors and emergency lights.
- Strip, seal, and wax vinyl tile floor covering.
- Lightly pressure wash steel panels to avoid corrosion if your building is near bodies of saltwater or facilities that use chlorine.
- Apply a high-quality siding wax to help maintain your structure’s exterior finish.
Doors & Windows
Here are a few modular building maintenance guidelines to keep in mind when inspecting your structure’s doors and windows:
- Ensure that rain diverters are preventing blowing rain from penetrating doors. This should be done every season.
- Clean sliding door tracks regularly to prevent dirt accumulation, which can interfere with its operation and cause premature wear on hangers.
- Clean hinges and hydraulic closers on swinging doors regularly to prevent dirt buildup, which can interfere with its operation and cause premature wear on hardware.
- Lubricate door closers and hinges every winter to avoid freezing.
- Caulk small gaps around doors and windows in the fall and spring.
- Inspect weatherstripping around doors and windows regularly for adjustment and damage.
- Clean sliding window tracks frequently and ensure their drain holes are kept open.
Flooring
Your modular building maintenance responsibilities should involve a thorough examination of your flooring. Be sure to:
- Trim carpet snags to prevent additional damage, and don’t seal rips or frayed seams with tape.
- Keep flooring free of dirt, standing water, melting snow, and ice melt salt.
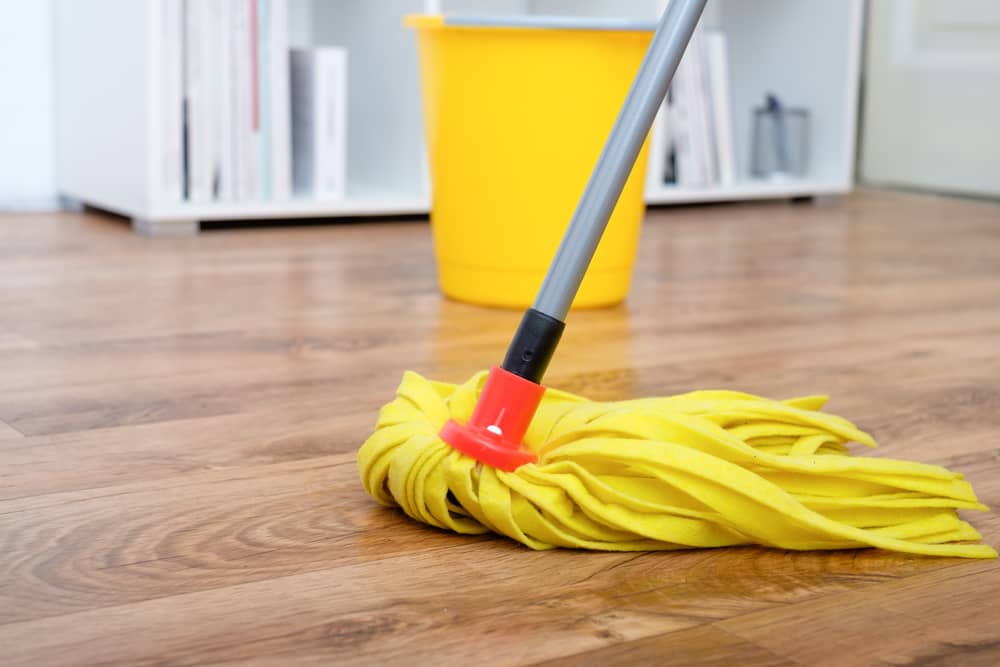
HVAC
Your HVAC system is one of the most important aspects of any commercial building maintenance schedule. Here are your most important jobs:
- Clean your HVAC air ducts every season.
- Keep supply registers open and ensure return air grilles aren’t blocked by furniture or decorations.
- Clean your A/C condenser coils over the summer.
- Have your heating system serviced in the fall and your cooling system serviced in the spring.
- Remove any objects blocking the skirting vents around the base of your building.
- Keep the thermostat no higher than 72 degrees F in the winter and no lower than 68 degrees F in the summer to avoid overworking your unit.
- Run your A/C in hot weather and during evenings, weekends, and holidays to maintain safe temperature and humidity levels. High temperatures and humidity produce excess moisture, which causes mold spores to grow and can degrade building materials.
Lighting
As part of your modular office care, it's important to include tasks that involve all your light fixtures:
- Replace fluorescent lamps, incandescent bulbs, and other lighting as needed. Try replacing with LEDs to provide a more energy-efficient option for your modular building. Clean light fixtures with acrylic lenses regularly to maximize output.
- Always replace light fixtures with two or more bulbs as a set. Rather than replacing them one at a time.
- Clean light fixtures with acrylic lenses regularly to maximize output.
Plumbing
Your building maintenance inspection checklist should involve the following plumbing-related tasks:
- Check plumbing fixtures for drips and leaks every summer.
- Clean drinking fountains every summer (if applicable).
- Wrap water lines in heat tape every winter to protect against freezing, breaking, and subsequent water damage.
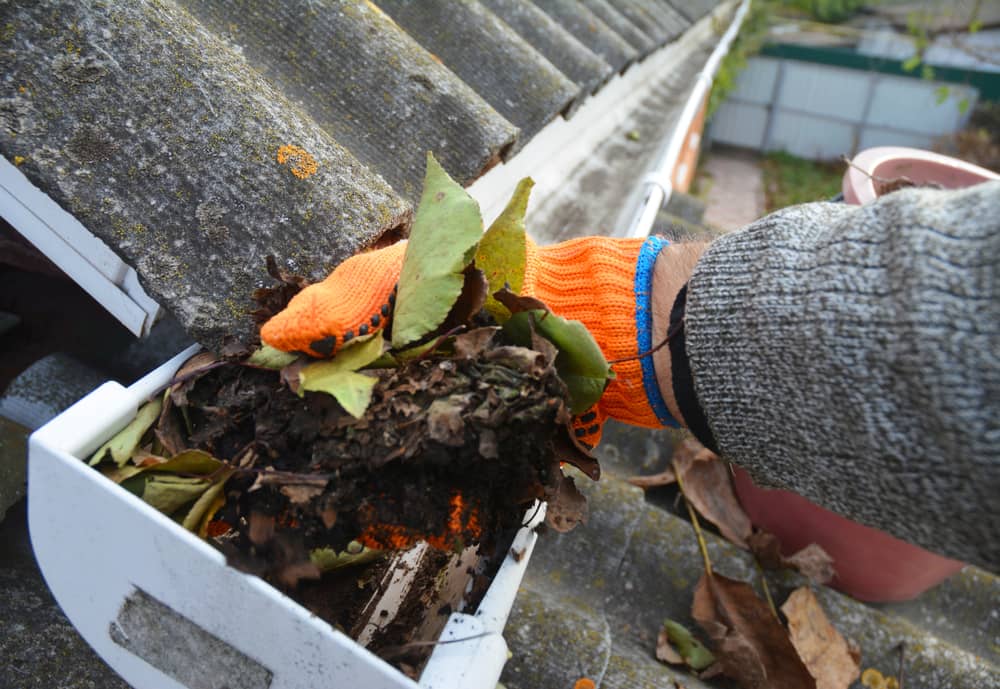
Roofing
It’s important to pay close attention to your modular structure’s roof and ensure it stays in good shape. Keep these essential building upkeep items in mind:
- Clear the roof of all debris, especially sharp items like nails, screws, stones, and branches.
- Inspect roofing for visible tears/cracks and loose/missing shingles in the fall and spring.
- Examine roof caulking for cracks.
- Remove snow as soon as possible to prevent leaks. If a leak does occur, dry the affected area immediately and use dehumidifiers to complete the drying process and prevent mold growth. Notify your dealer of any leaks.
- Ensure adequate storm drainage to eliminate any chances of pooling water.
Siding
Here are a few modular building maintenance responsibilities to keep in mind when examining your structure’s siding:
- Inspect siding for cracks, chipping, and scratches and touch up damage as necessary.
- Caulk siding materials and window frames as needed to prevent water penetration.
- Lightly pressure wash steel panels every year to avoid corrosion if your building is near bodies of saltwater or facilities that use chlorine.
- Wash siding paint regularly with a mild detergent and cold water. Never use sandpaper, steel wool, or mineral acids on paint.
- Apply a high-quality siding wax every year to help maintain your structure’s exterior finish.
Miscellaneous
These miscellaneous modular office building maintenance checklist items help keep your structure in tip-top shape:
- Don’t remove inspection labels from walls, doors, windows, and electrical panels.
- Institute and maintain a pest control program to protect against insects and rodents.
- Examine the soil under your building after heavy rains to ensure that it’s still level.
When to Contact Your Modular Builder Immediately
There are times when you’ll need to call a professional for your repair or maintenance. For less urgent modular office repairs, we can connect you with one of our local vendors. However, if it is urgent, we recommend using your regular vendor.
The following problems should be addressed as quickly as possible:
- Plumbing Leaks
- Roof leaks from rainwater or snow
- Tears or cracks in the roofing material
Modular Building Inspections
Understanding how modular building inspections work (and what happens before your structure leaves the factory) goes hand-in-hand with completing your modular office care responsibilities.
One of the biggest misconceptions about modular structures is that they don’t have to undergo inspections, but this isn’t the case. Modular buildings are subject to the same building codes as traditional construction projects.
In fact, modular office building construction requires more rigorous inspections than traditionally-built structures because they must withstand transportation to the jobsite and craning installation.
The Modular Building Institute and the International Code Counsel developed some guidelines that modular companies can use to ensure consistency and compliance with a global standard.
Modular structures undergo comprehensive inspections at each stage of the design and build processes. We’ll take a closer look at each of these below.
Stage 1: Design
Once your modular building drawings and specifications are complete, they’re sent to third-party engineers for review to ensure they meet all applicable federal and state building codes. Any necessary revisions must be made before manufacturing can begin.
The Uniform Construction Code has a set of requirements for plan review and inspections for your modular structure. Your modular provider will be able to help you sort applications, fees, and specifications.
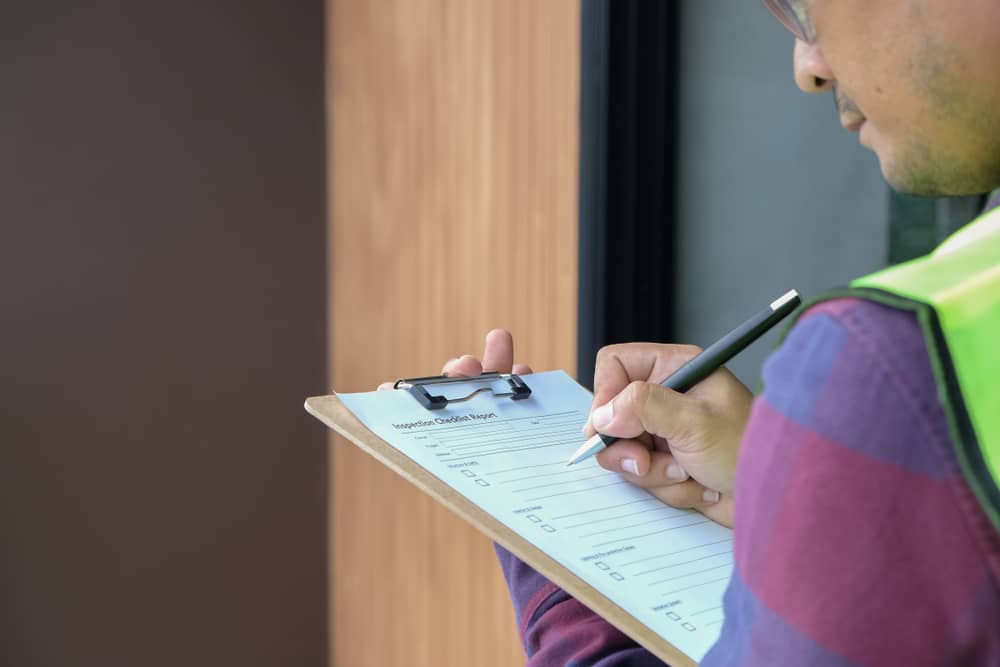
Stage 2: Before Delivery
Because they’re fabricated in sections via an assembly line system, modular buildings receive frequent inspections and testing. This controlled environment also maximizes efficiency and productivity while ensuring structures of the highest quality. Additionally, non-compliance issues can be caught and corrected without affecting other areas of the building process.
Modular structures are evaluated based on the building codes applicable to where they’ll be installed. Temporary structures that will be used in several locations are evaluated and inspected to meet regulations for several states simultaneously.
Once all approvals have been provided, proof of compliance (usually a tag or seal) is applied to each module before it’s shipped to the jobsite.
Stage 3: After Final Assembly
Finally, third-party inspections are performed during final on-site assembly to ensure your modular building is safe, durable, and ready for occupancy. These inspections cover items like:
- Site connections that hold the modules together
- Building foundation
- Site utility work
- ADA compliance
- Fire protection and suppression
- Life safety
- Issues with surrounding land (e.g. water runoff)
International Building Code (IBC) Requirements
Modular structures must also meet International Building Code (IBC) requirements, in addition to all applicable state and federal building codes. Modular structures fall into two IBC construction types:
Type V-B and Type II-B.
- Type V-B structures feature unprotected wood frames built with standard lumber.
- Type II-B structures are non-combustible and are often made from steel.
Modular Building Permits
Building permits are the final piece of the puzzle when it comes to inspections and modular building maintenance guidelines. Building permits are required for both new construction and major renovations of modular structures, and each region of the country has different requirements.
Most modular construction permits can be broken down into the following categories:
- Foundation
- Mechanical
- Electrical
- Plumbing
- Road opening
- Water/sewer
- Fire suppression
The first step in a strong modular structure is finding a company that understands the ins and outs of modular building inspections. Using our building maintenance inspection checklist can then help you extend your modular structure lifespan and keep it looking brand new.
Ready to design a new structure or renovate your existing space? BOXX Modular is here to help. Contact us today for a free quote and to connect with your local dealer.
Ready to solve your space needs?
Modular buildings are the way to go. Request a quote or contact us today to get the conversation started. We’d love to talk to you about how modular can meet — and exceed — your needs.