Modular Construction vs Traditional Construction: What’s Better for Your Business?
The reason for a new structure can vary. Maybe your business is growing and your space needs to be expanded, or you’re testing your product in a new target market and you need temporary space, or maybe a new structure is needed unexpectedly and you need it fast.
Whatever the case may be, have you considered the differences between modular construction vs traditional? You may be surprised to find that modular construction can be easily adapted to meet your specific structural goals, in half the amount of time.
Restrictions to Traditional Construction Methods
A high percentage of conventional construction methods must take the following factors into consideration.
- How much time will you be on-site?
- How will the timeline change when bad weather occurs?
- How will this project disrupt the natural flow of your organization?
Below, we list out common traditional construction methods and the limitations that come with each.
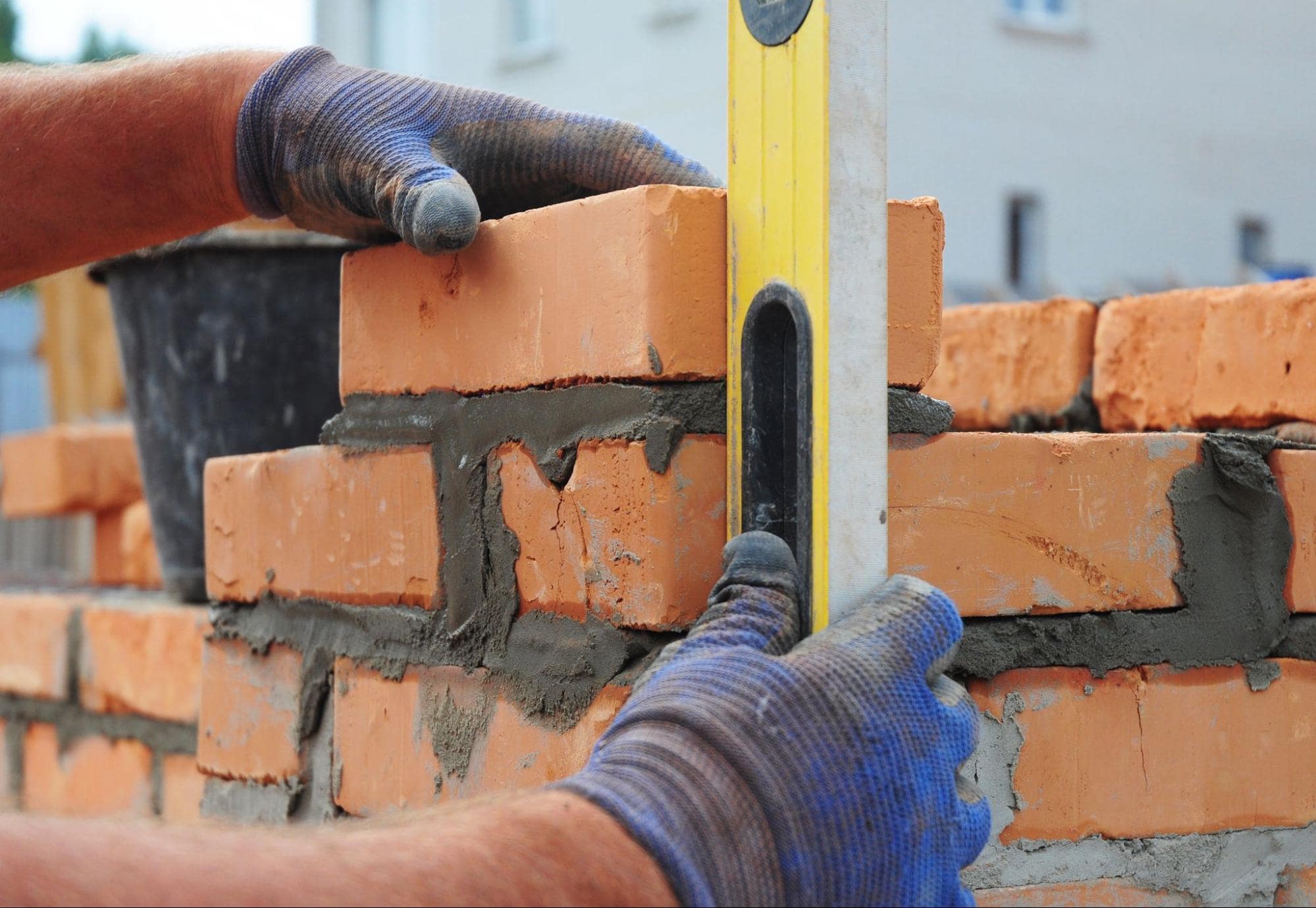
Brick & Mortar
Masonry work is a very labor-intensive process because you have to individually place each brick. With a significant labor shortage within the construction industry, this becomes a much bigger problem. Your construction company would have to pay for this labor-intensive job that would likely include overtime work to finish the project on time.
Additionally, brick masonry is more susceptible to seismic damage. This material isn’t as durable as other traditional construction methods, so the building is likely to need repairs down the line.
Concrete
Similar to brick masonry, concrete buildings require a lot of labor to get the job done. Because of the materials and labor, the pricing of this type of project can be difficult to determine prior to the start of production. This could potentially lead to unexpected costs along the way.
In general, concrete has a high compressive strength but low tensile strength which leads to chipping and cracking. So, over time you will have to spend time and money on repairs to your structure.
Wood
Compared to brick and concrete masonry, wood framing requires more engineering and skill on site. Ultimately, the lack of experience in the workforce can cause limitations in quality control for wood-framed buildings.
Like a majority of traditional construction methods, your project faces the potential to be delayed when harsh weather conditions come through. When wood is exposed to excess moisture or heavy rain, the materials become susceptible to decay.
Easily see the differences of each building material by downloading our Traditional vs Modular PDF.
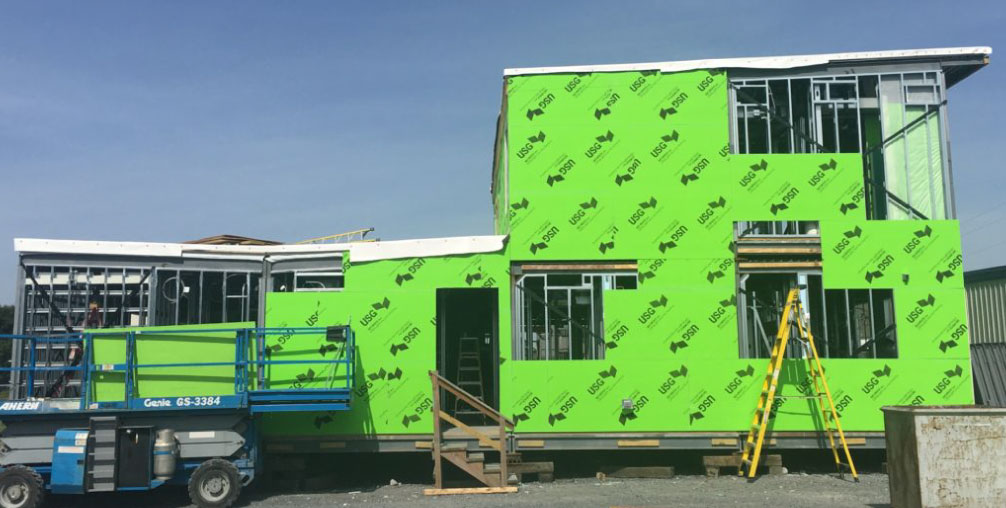
7 Distinct Differences Between Modular and Traditional Construction Processes
Now that we’ve laid out the traditional construction methods, how do they compare to modular construction? Below, you’ll find significant advantages of modular for not only your organization but for the surrounding environment.
1. Time on Site
Your work days are busy and a time to be productive. And when a construction site is right outside your window, it can be distracting and difficult to focus on the work you need to complete.
Conventional construction sites can bring many distractions, loud noises, and dust to your work surroundings. We’ll discuss this more in the next point, but ultimately a disadvantage of conventional construction is the disruptions that come with on-site procedures.
Another consideration is how many people are on-site during your construction project. The more people you have on-site, the higher chance of human errors and injuries. And as we’ll talk about later, there’s likely already a limited amount of workforce, so injuries are even more costly.
2. Interruptions to Work Flow
One of the most significant advantages of modular construction is that a majority of the work is done off-site in a manufacturing facility. What does that mean for your company? There are fewer distractions to your organization and you can continue to generate profits during your construction project.
Less time on-site also means fewer interruptions to communities and businesses around you. When you start a construction project, it often means you’ll have to close roads, fence off parking lots, and create a lot more commotion. These disturbances could negatively affect your business’s reputation and camaraderie with surrounding organizations and the local community.
3. Pricing
In construction projects, there are typically four different elements you’ll need to consider when you’re projecting a budget.
Materials. This includes quantities of each building material, for every phase of the construction process.
Labor. This is a large chunk of your budget and should be calculated through a predicted amount of hours expected for each phase of the project. In conventional construction, you’ll need to estimate for emergency workers and overtime if, and when, unexpected challenges arise.
Equipment. If the company owns a lot of the required equipment then this portion of the budget will be relatively small. Aside from the physical equipment, they will also need to budget for transportation and maintenance costs.
Overhead. The final section of your budget will cover all additional costs including manager salaries, permit fees, and on-site costs.
When looking at the four sections above, you can greatly minimize each cost by choosing modular construction vs traditional. The benefit of having your building modules constructed in a controlled environment reduces the number of logistical delays that are often followed by more costs.
The labor for a modular project is consistent and specialized so you won’t have to worry about shortages or overtime. Also, BOXX Modular facilities have the equipment we need to complete your structure to meet your expectations.
Ultimately, there is more stability in a modular construction budget compared to conventional construction budgets.
4. Quality
Generally, a construction site has a lot of moving factors and is bustling with equipment, workers, and noise. As a result, this can lead to miscommunications and human errors that will set your timeline back and cost your organization money.
Since the modular construction process is in a controlled environment, you will have well-trained employees producing your modules. There is greater supervision and specialization within the labor force.
Ultimately, the assembly line process means that the quality control of your module will be better compared to conventional construction methods.
5. Sustainability
On average, a 2,000-square-foot construction project that uses traditional construction methods will generate about 8,000 pounds of garbage for a landfill. On top of that, the construction industry contributes large percentages to air and water pollution.
Combining actions taken on the construction site, transportation of materials and equipment, and the manufacturing process of building your structure, produces 39% of total carbon dioxide emissions.
With a controlled environment, there is more precision with building materials and ultimately less waste on your project. If there are extra materials, these can be easily stored and reused in future projects rather than going straight to the landfill.
6. Labor Security
As we’ve stated in the pricing section above, a significant advantage of modular construction is the labor security that comes along with it. As a whole, the construction industry is facing notable shortages.
First, the workers that have spent years in the industry are getting older and retiring. And the upcoming workforce isn’t interested in entering a labor-intensive field with longer hours. As a result, the amount of labor leaving the industry isn’t being fulfilled by new, motivated workers.
What does this mean for your construction project? It’s likely there will be shortages and extra costs to pay the workers for overtime. Additionally, the workforce may become burnt out leaving the job to a newer, and greener, workforce, so human errors may occur throughout the process.
A key difference between modular construction vs traditional is the amount of workforce you need to complete a structure. Customarily, modular facilities are located in centralized locations with a diverse pool of labor, so there isn’t a shortage of skilled workers.
These workers are also consistently in one area rather than traveling to different sites, which helps make a modular construction job more appealing compared to a traditional construction job. With a modular construction project, you will only be responsible for site preparation and final installation. We’ll take care of the rest, including shipping your structure directly to you.
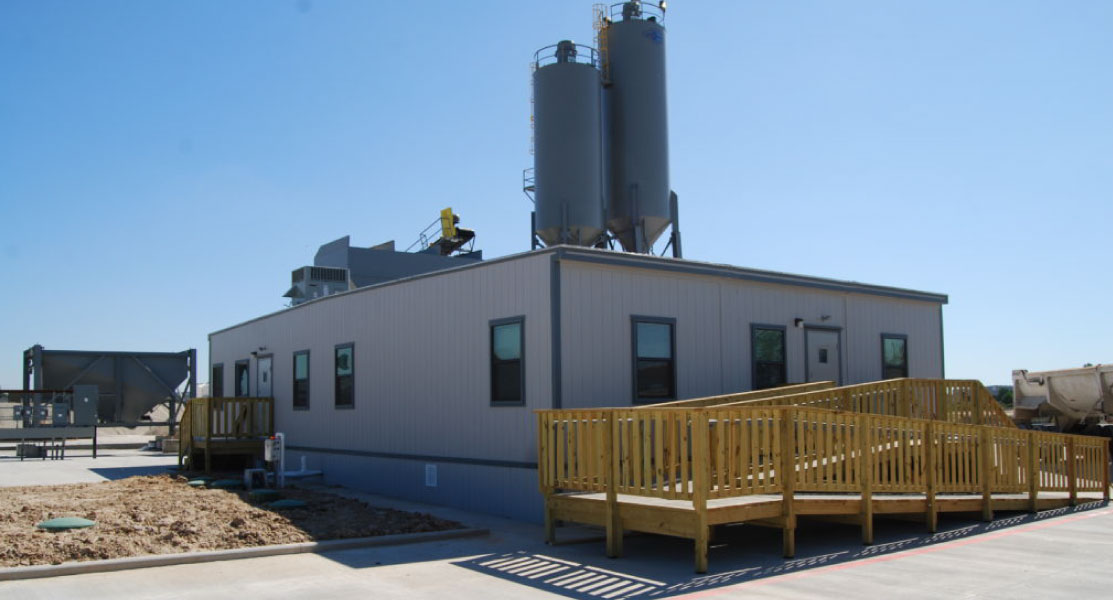
7. Building Longevity
There are times when you need a structure fast and don’t want to deal with it forever. For example, maybe you’re a school principal and you’re noticing that classrooms are becoming overcrowded and students aren’t getting the best learning experience. If that’s the case, you probably don’t have time or the ability to renovate your permanent building without pausing school and disrupting workflows.
To help meet the needs of your school population, consider modular construction. Modular buildings are produced up to 50% quicker than conventional construction buildings, and can be used for as long, or as little as you need.
The purpose of modular is that it can be quickly disassembled when you no longer need it, or easily transported to a more resourceful location. Now, this doesn’t mean that your building will be less durable or structurally sound. In fact, with proper care, your modular structure can last as long as a conventional counterpart.
At BOXX Modular, we also have a select inventory of used modular structures for an even more efficient installation. This will not only help you save time and money in urgent situations but can contribute to building a greener future.
Consider modular construction vs traditional and which would better align with your organizational goals and objectives. Modular can either be a temporary solution for your problem or be a stepping stone until you’re ready for your permanent structure.
Easily see the differences of each building material by downloading our Traditional vs Modular PDF.
Ready to solve your space needs?
Modular buildings are the way to go. Request a quote or contact us today to get the conversation started. We’d love to talk to you about how modular can meet — and exceed — your needs.