Living a green lifestyle is becoming more and more popular as worries about the future of resources and our own environmental effect grow. Today's consumers prioritize eco-friendly elements in new construction, which has sparked innovation in building materials, methods, and more.
The modular construction sector focuses on environmentally friendly building construction that reduces waste, maximizes material utilization, and uses a more sustainable and efficient approach in order to reduce these worries.
Trouble With Traditional Construction
According to an article published by Archdesk, the construction sector contributes to 23% of air pollution, 40% of drinking water pollution, and 50% of landfill waste.
A 2,000 square foot building constructed using conventional on-site techniques will generate about 8,000 pounds of garbage for the landfill. On the flip side, off-site modular construction recycles or reuses surplus materials for later projects. This in turn lowers the volume of waste that ends up in nearby landfills.
Not only does it cut back on landfill waste, but modular buildings can be used time and time again over their lifetime. It is a building that can truly be recycled at the end of its life with one customer, and repurposed and given a new life with a new customer.
How Does Modular Differentiate from Traditional Construction?
With traditional construction methods, buildings are typically built on-site, from start to finish. Which means that contractors create the entire structure in its final location. Keep in mind, that that implies everything is done on site, in the outdoors.
However, modular construction methods actually produce buildings off-site in a manufacturing facility, and then assemble them afterwards.
Factory employees erect modular buildings in sections (or modules) using an assembly-line method so they can work on numerous building components at once. The components are designed to be easily assembled later, much like building blocks or LEGOs. This overall has a huge environmental benefit, because the elements are controlled and less materials are wasted.
Although modular construction may appear to be just a new or contemporary method of construction, it actually has distinctive qualities that make it more environmentally and sustainably friendly.
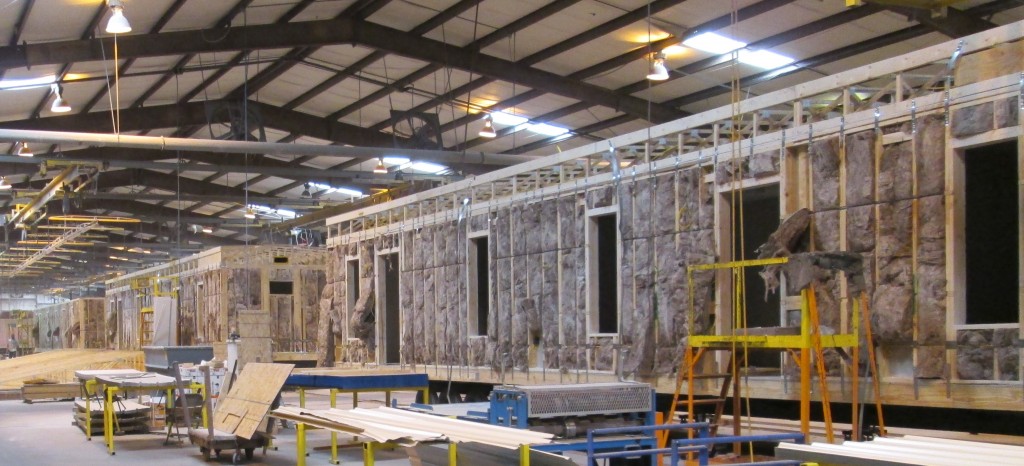
Does Modular Have What It Takes?
But does the modular industry have the potential to help the construction industry meet its ever-increasing sustainability goals? We believe it does.
Proponents of modular construction do too, arguing that it can deliver greater environmental and social sustainability benefits than conventional construction can. Common claims for the sustainability benefits of modular construction include:
- reduced material waste
- reduced disruption to the building site and surrounding community
- safer working conditions
- reduced operational energy
In a report from BuildingGreen, they examined the potential benefits of modular construction in depth, in order to provide a better understanding of the potential benefits through modular's design methods and project management.
8 Sustainable Benefits of Modular Construction
the following information is taken from BuildingGreen.
1. Efficiency and Quality Control- with modular construction, the bulk of fabrication and assembly of building components is done primarily in a controlled, factory setting. The process of design, manufacturing, and construction are both tightly integrated, and fully optimized to create efficiency and quality assurance.
2. Reduction in Material Waste- Modular construction could cut net waste in half compared to conventional construction. The optimized conditions of the fabrication facility result in a reduction in errors, accidental damage. Factory-based modular construction processes are also better able to implement lean production principles and other strategies to better-control inventory.
3. Reduction in Energy Use- Construction energy can be reduced during the fabrication phase of a modular project because factories are better able to control energy use and emissions than their traditional counterparts. Modular projects require fewer workers on site, for a much shorter period of time, so onsite energy use will be much reduced. Not only that, but the robust structure of modular buildings supports a longer life cycle, so the energy and carbon cost of its construction can be amortized over a long period of time.
4. Reduction in Operational Impact- Due to the science behind factory-based building methods, and thermal performance, operational costs can be cut by 15-20%.
5. Support of Adaptation, Reuse, and Recycling- Modular construction allows for a kind of "plug and play" flexibility that allows buildings to be easily and affordably adapted, modified, and reused or de-constructed for recycling. Modular construction makes building more flexible and adaptable, and therefore more "future-proof".
6. Reduction of Indoor Environmental Quality Issues- The factory-based production of modular building components allows for a longer period of off-gassing of VOCs from adhesives, sealants, and finishes before occupancy. The potential for high levels of moisture to collect in materials is much less likely when the building's components are produced in a factory.
7. Improved, Safer Working Conditions- Compared to its conventional counterpart, modular construction in an offsite facility is generally safer for workers. Workers in a modular fabrication facility are exposed to fewer risks than workers on a conventional building site, where they are generally required to working outdoor conditions, in the presence of heavy machinery, and at height.
8. Reduction in Disruption to Surrounding Community- Modular projects generally have a smaller construction footprint than conventional projects and generally require less space around the project for workers, truck traffic, and material storage. The onsite portion of the process also lasts for a much shorter tie, so there is less disruption o the neighboring community in the form of noise and air pollution.
Paving the Way Forward
When it comes to green building solutions, the Whitehouse recently made a zero-net target for carbon emissions by 2050, including a Buy Clean policy to promote use of construction materials with lower embodied emissions. With this legislation in place, it may be a good time for companies to consider modular construction methods.
How about you? Have you already implemented some eco-solutions? Or are you looking into sustainable building methods for your next construction project? If so, give us a call or request a quote today! 877-966-7839
Ready to solve your space needs?
Modular buildings are the way to go. Request a quote or contact us today to get the conversation started. We’d love to talk to you about how modular can meet — and exceed — your needs.