Why Choose Modular Construction: Top 7 Questions About Modular Answered
The world of modular is vast and still a fairly new possibility for a lot of commercial companies. So when you aren’t as familiar with this type of process, the question becomes, why choose modular construction? What are the benefits of modular? What are the disadvantages?
By learning more about modular construction and its capabilities, you’ll be setting your organization up to become more adaptable for the future.
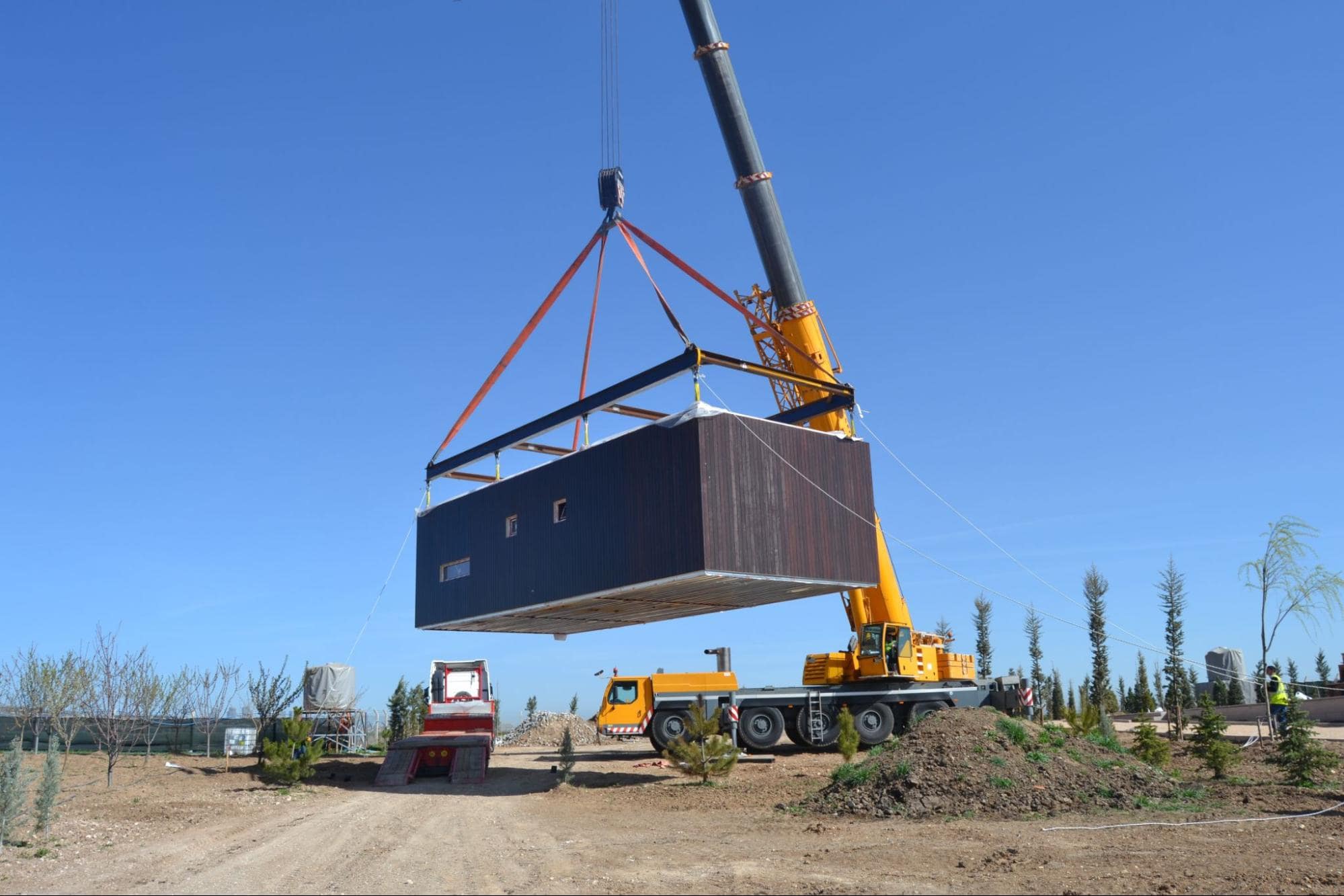
1. What is Modular Construction?
Unlike traditional construction, modular construction involves producing a building off-site in a controlled environment. Then, when each module is ready they are transported to your site for installation. The building codes and standards are the same compared to other building types.
Because a majority of the work is done off-site, the construction process is much quicker within a controlled environment. Specialized workers who are highly skilled in their area of expertise are overseeing each step of the assembly process, making everything more precise.
Modular construction can be used within almost any industry and is beneficial for the following scenarios:
- Your organization is growing.
- You’d like to make renovations to your existing building without shutting down or losing revenue.
- You need a temporary space during permanent renovations.
- You want an organized workspace for your contractors.
- You’re a new organization.
- Your organization wants to test a new market in a different location.
2. What is the Life Expectancy of a Modular Building?
A considerable benefit of modular is the flexibility and adaptability you have to use the building for as long as it is valuable to your organization. Depending on your situation, you may need a building for a few months or years, or need to use the structure as a more permanent building.
Typically, commercial modular buildings are looked at as standardized and used for a short period of time. However, even if you opt for a temporary building, the life expectancy is still up to 30 years if it’s well-maintained.
Permanent buildings, which have a slightly different installation process, can last just as long as their traditionally built counterparts. So, if you need a structure for a significant period of time, you can be confident that a modular building would be a viable option.
Within the modular world, you can also choose to buy a building outright or lease the structure. This factor continues to support the fact that the life expectancy of a modular structure truly depends on how long you need the building.
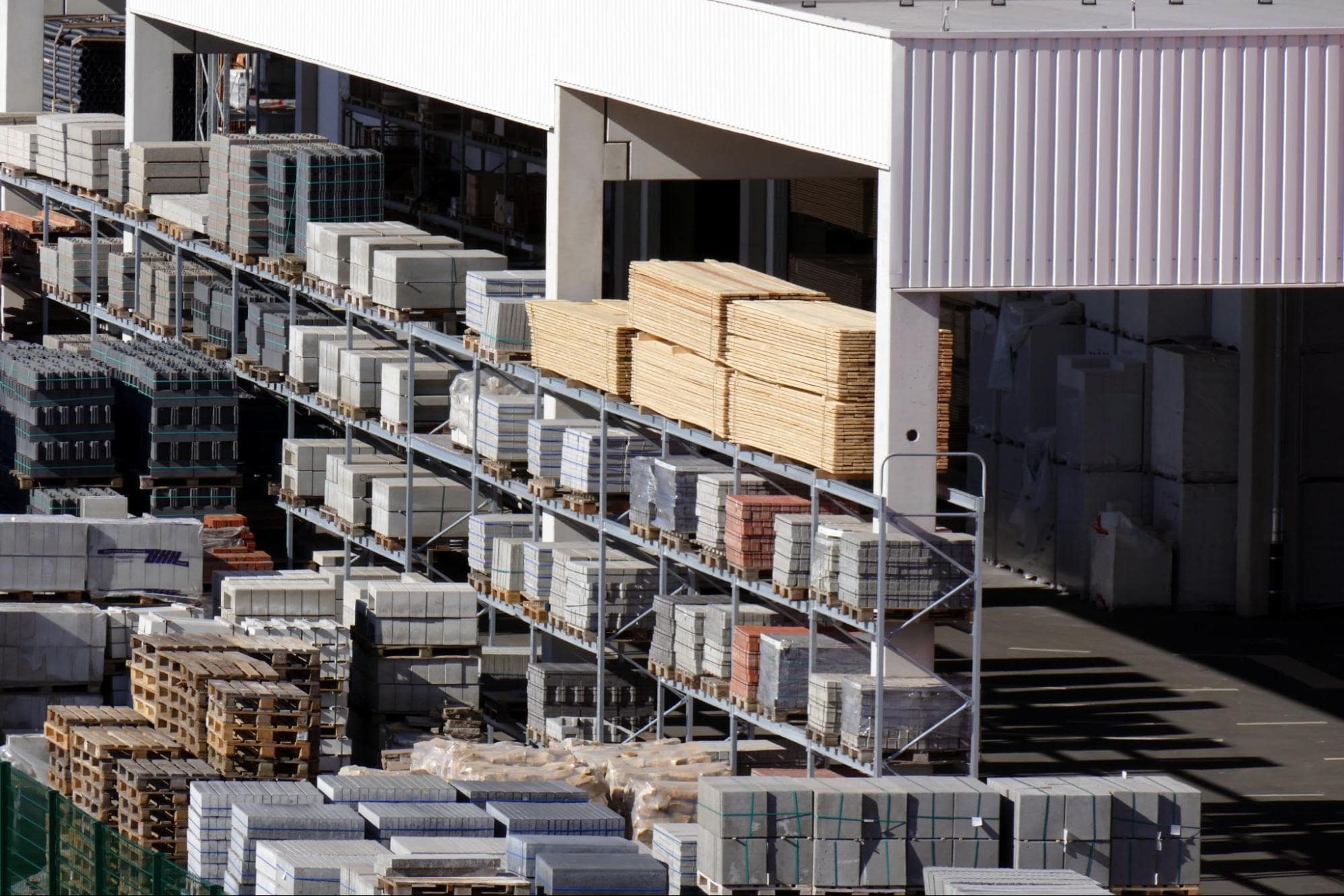
3. How Does a Modular Building Compare to Other Structures?
There are multiple ways that modular structures distinctly differ from traditional construction. As answered in the first question, “What is modular construction?”, the main difference is that a majority of the construction process is completed in a controlled environment.
Another significant difference between modular construction and traditional construction, is building longevity. Compared to other structures, you will have more control over how long the building is used and how long you’re paying for it.
Modular buildings can hold up just as long as other structures and be completed in half the time. These types of buildings are built to meet the same building standards and codes as traditional structures.
Additionally, modular buildings can be completely customized to look and feel like any other building. So, there’s very little difference between modular and other structures, once the building is completed.
4. How Energy Efficient Are Modular Buildings?
Minimal waste is curated during the construction process of a modular temporary building because there is a higher level of supervision in a controlled environment. This makes modular construction a sustainable and energy-efficient option, especially compared to traditional construction methods.
On the other hand, traditional construction contributes large percentages to pollution and landfill waste. This is largely due to the amount of equipment, vehicles, and materials used during the project.
Additionally, the design flexibility of modular buildings allows for them to be easily disassembled and reused. This creates a more sustainable construction process because customers have the ability to rent used buildings for temporary swing space.
Commercial modular buildings from BOXX Modular are consistently in line with LEED certification standards because of their limited energy and water use as well as the reduction of greenhouse gas emissions.
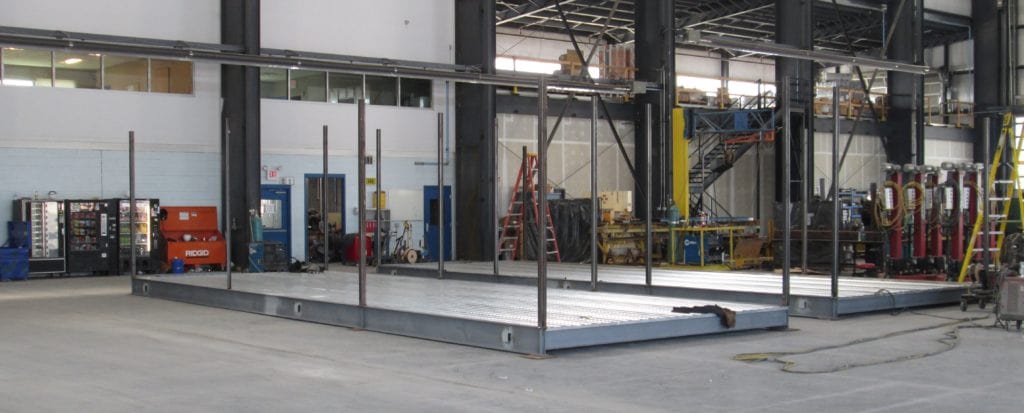
5. What Materials Are Used in Modular Construction?
When designing your commercial modular building, you have different material options. Below, we’ll highlight some of those choices when it comes to the framing, interior, and exterior of your building.
Framing Materials
Depending on the purpose of your modular building, it can be made from either a wood, steel, or concrete frame.
Manipulating wood is very easy, so we are able to mold the shape and size of your structure to match your needs. Modules made from wood use traditional studs and standard lumber. Wood is the more sustainable option among the different materials because it is biodegradable, recyclable, and provides high insulation for low energy loss.
On the other hand, a steel or concrete frame may be used if you need a fire-resistant material. This material also has the ability to be recycled. In fact, up to 80% of your concrete frame could be recycled materials.
Interior Materials
Inside your modular structure, you’ll have choices of what materials are used. Typically, vinyl composite tiles are used for high-traffic areas and ceramic tiles are used for areas with high humidities, such as a bathroom.
In some cases, like a portable classroom, a customer may opt for carpeting. This creates a safe and comfortable environment and reduces noise between each module. The final floor option is vinyl plank flooring, which provides a sophisticated look but is easy to maintain and install.
Exterior Materials
You’ll notice there are a lot more options when it comes to the exterior of your structure, so it’s especially important to understand the purpose and location of your commercial modular building.
Stone Veneer. If your building needs to blend in with a larger campus, you should consider a stone veneer material. This is a very customizable material so your organization can match your existing buildings.
Composite Exterior Panels. If you need a temporary building within a construction site, you might not be as invested in customizing the exterior. In that case, you should consider a composite exterior panel because they are cost-effective, and can be quickly applied to either wood or steel frames.
Vinyl. Another popular choice is vinyl because it can be fully customized and is a very durable material. This is an ideal choice for a structure that needs to withstand multiple outdoor elements and conditions.
Stucco. Stucco is a low-maintenance material that can be used in a wide variety of climates and conditions. It is one of the most cost-effective options and has a lifespan of over 50 years when well-maintained.
Thin Brick. Compared to traditional brick, thin brick is a lighter option that doesn’t have as many seismic concerns. This material also provides fire resistance compared to other modular materials.
6. What Are The Disadvantages of Modular Construction?
In the past, there were some misconceptions about modular construction, leading to a few perceived disadvantages. However, these misconceptions are gradually being proven wrong as modular gains popularity.
Despite only accounting for 4% of the market, it is as high quality and structurally sound as traditional methods. Any perceived disadvantages are mainly due to outdated information and limited use, which will likely be resolved as the industry continues to evolve and improve.
7. How Much Does it Cost to Build a Modular Structure?
The specific cost of your modular structure will depend on the materials you choose, your interior set-up, and any additional customizations. However, we can give you an estimate to compare to other construction methods and budgets.
One of the bigger advantages of a commercial modular building is that the cost is more stable than traditional construction methods. It’s not a secret that the construction industry is facing a serious labor shortage which will ultimately affect your budget and timeline.
Generally, you can find a breakdown of project costs to include the following
- Hard Costs
- Soft Costs
- Vendor Costs
- Operational Costs
You can see a more in-depth breakdown of BOXX Modular costs by downloading our How Much Do Modular Buildings Cost PDF.
Have more questions on why you should choose modular construction?
Ready to solve your space needs?
Modular buildings are the way to go. Request a quote or contact us today to get the conversation started. We’d love to talk to you about how modular can meet — and exceed — your needs.