Offsite Construction. Prefab. Modular. Are They the Same Thing?
Yes. And, no. We all know the old elementary school lesson that all rectangles are squares, but not all squares are rectangles? That’s the same concept at work here.
Offsite construction is the larger umbrella term which many other types of construction fall under. There are two types of offsite construction: Prefab and Manufactured. Additionally, there are two types of prefab construction: Modular and Panel Built. Even more, there are two types of modular buildings: Relocatable and Permanent.
So, as an example, all relocatable modular structures are built utilizing offsite construction, but not all offsite construction is modularly built. Are you following?
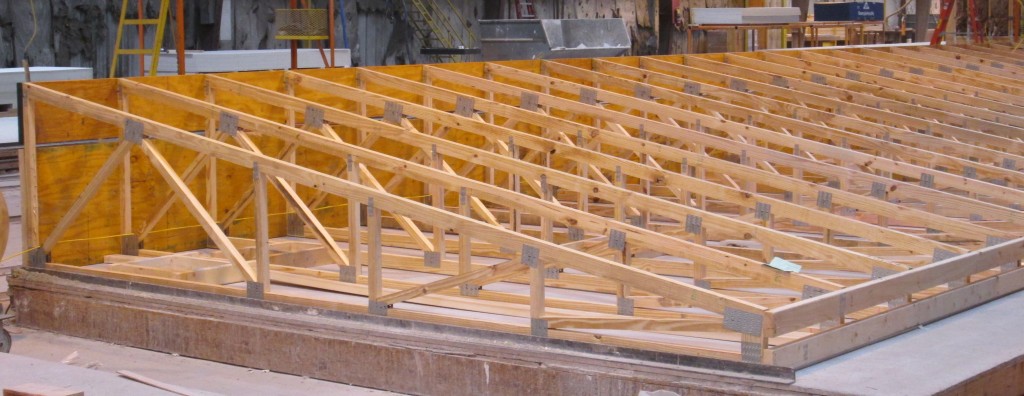
What Do They All Mean?
Off-site construction involves the process of planning, designing, fabricating, transporting, and assembling building elements away from your final build site for rapid site assembly.
Prefab
Sections of the structure are built in a factory then assembled on site. The process must adhere to state and federal building codes and undergo regular inspections.
Modular – The building is constructed in separate box-like modules which are transported and then secured together onsite to form a whole. The modules are transported on flatbed trucks and pieced together on-site.
Relocatable – This option is for temporary space needs like job site trailers, temporary classrooms, communication pods, and showrooms.
Permanent – These can be multi-story buildings, government buildings, hospitals and healthcare facilities, schools, and hotels.
Panel Built – This type of structure is accomplished by laying down the floor and then lowering each section of the wall in to place one at a time. Commercial prefabricated buildings are often done this way as it allows for wide-open spaces and high ceilings.
Manufactured
This type of off-site construction is built on a steel frame, shipped on its own wheels, and then laid on a crawl space, or a slab of concrete. In some cases, the wheels that got the house to the building site aren’t even removed, just covered up with side skirting.
Why Choose Offsite Construction?
Projects that are restricted by a time schedule revenue are perfect for offsite construction. Such as:
- Schools and dormitories that must open for a new school year or semester
- Retail units that must open doors to gain an increased return on revenue
Repetitive projects such as identical classroom units, dormitory units, office units, laboratories, high-tech facilities, communication structures, and bathroom pods, are good options for offsite construction.
Additionally, projects that employ unique forms, unique sustainability requirements, or a higher degree of control in the end product also benefit from offsite construction. The factory provides space for prototyping, quality control, and the ability to integrate complex systems.
With on-site construction, it’s difficult to monitor the quality of work being done by each contractor. With offsite construction, the quality of each part and section is ensured because each one is created in a factory setting where work is streamlined to each expertise.
Whatever you call it off-site, prefab, or modular construction, we welcome the opportunity to partner with you! View our project gallery or contact a modular building expert in your area.
Ready to solve your space needs?
Modular buildings are the way to go. Request a quote or contact us today to get the conversation started. We’d love to talk to you about how modular can meet — and exceed — your needs.