How Modular Building is Playing a Role in Reducing Construction Waste
With nearly 40% of the nation’s landfill waste coming from construction materials, there has been a recent rise of green builders whose focus is on reducing and repurposing waste in the construction industry. However, modular construction has long been a front-runner in the field of green building and reducing construction waste through off-site operations that result in efficient inventory control, material reuse, automation of tasks, and delivery.
The Trouble with Traditional Construction
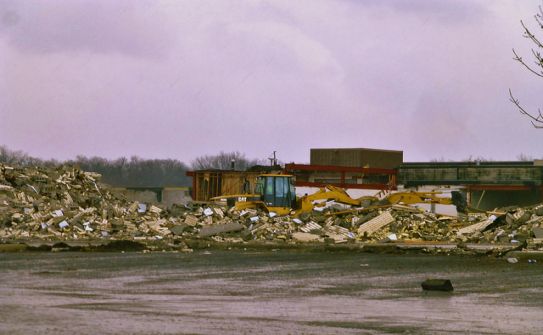
Figures developed by the U.S. Environmental Protection Agency (EPA) help us truly understand the sheer amount of construction and demolition (C&D) waste produced with each project. In commercial construction, new buildings generate an average of 3.9 pounds of waste per square foot. Looking at a mid-size office building or college residence hall, approximately 50,000 sq. ft., almost 100 tons of waste will be produced during the project. If the project includes demolition, the same 50,000 square foot building will result in almost 4,000 tons of waste (155 pounds per square foot).
Some of the biggest waste deposits in traditional construction are:
- packaging (up to 5%)
- timber (up to 25%)
- plasterboard (up to 36%)
While progress is being made to make traditional construction more sustainable, the EPA still estimates that 88 million tons of C&D waste are added to landfills each year.
Modular Construction – Reducing Construction Waste by 90%
Modular construction has been providing an environmentally responsible alternative for over 40 years. The off-site construction methods used in modular building focus on efficient and sustainable building methods that result in reducing construction waste, maximizing material use and a more streamlined output process.
In contrast to the staggering amounts of waste produced using traditional construction methods, a report from WRAP (Waste & Resources Action Programme) shows that a 90% waste reduction can be achieved by increasing the use of off-site construction.
With off-site modular construction, module units are assembled in controlled conditions. This allows for minimal material waste associated with weather conditions and construction site theft. As the off-site elements of the construction projects conclude, largely finished modular units arrive at the construction site, significantly limiting construction waste generated on the project site.
Built for Deconstruction and Reuse
Modular building systems are a prime example of a growing adaptable reuse movement. They are flexible, adaptable, and reusable. They are essentially built to be unbuilt.
The amount of waste produced when deconstructing a modular building is tremendously less than an outdated building that needs to be demolished. The adaptable and reusable nature of modular structures reduces the need for additional raw material and minimizes the energy necessary to create a building from existing modules.
If you’re looking to make a positive impact on the environment through your next expansion or new building project, consider modular building. Talk to a modular expert in your area.
photo credit: https://www.flickr.com/photos/35740357@N03/3952618003
Ready to solve your space needs?
Modular buildings are the way to go. Request a quote or contact us today to get the conversation started. We’d love to talk to you about how modular can meet — and exceed — your needs.